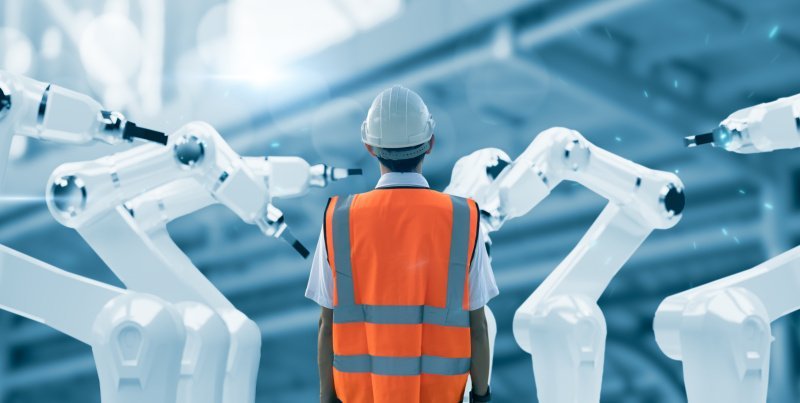
Петр МИШНЕВ, директор по техническому развитию и качеству ПАО «Северсталь»:
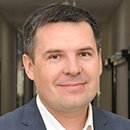
Наша компания первой среди российских металлургических предприятий реализует масштабный проект, направленный на повсеместное внедрение автоматизированной системы контроля качества (АСКК), использующей в том числе такие инструменты, как нейросеть и «компьютерное зрение».
Прежде в компании существовало большое количество технологических параметров и внутренних правил принятия решений о годности продукции. Но при использовании исключительно традиционных методов контроля единственным вариантом была выборочная проверка товарных партий. Однако учитывая, что на данном этапе мы значительно расширили линейку новых видов продукции, появилось множество новых клиентов, а прежние повысили уровень требований — все это и стало предпосылкой для запуска АСКК, с помощью которой сегодня уже контролируется выпуск порядка половины ежегодного объема производимой металлопродукции.
В новое решение мы включили такие составляющие, как измерители, отвечающие за фиксацию видимых дефектов, прогнозные модели с расчетом вероятности возникновения невидимых недостатков на основании технологических параметров, систему слежения за металлом, в которой осуществляется привязка данных к метру продукта, и систему автоаттестации Sherlock, применяемую для принятия решений по аттестации продукции и транслирования их персоналу.
Нам важно было гибко интегрировать отдельные подсистемы в единую систему, в которой будет контролироваться каждый дефект, когда-либо обнаруженный клиентами в нашей продукции. Так, внедренная система инспекции поверхности способна автоматически выявлять и классифицировать поверхностные дефекты металлопроката, выпущенного в производственном потоке. Также она обеспечивает возможность выявления корневых причин получения несоответствующей продукции.
Система измерения геометрии обеспечивает контроль геометрических параметров готовой продукции, произведенной на оборудовании стана, исключая тем самым отправку на последующие переделы производства и клиентам некачественного металла, а также обеспечивает снижение времени аттестации.
Система фиксации инцидентов следит за возникновением инцидентов в критических зонах, влияющих на качество продукции. Это позволяет исключить человеческий фактор в вопросах, касающихся корректной работы оборудования, а также своевременную реакцию на отклонения в технологических процессах.
Упомянутая уже прогнозная аналитика позволяет на основании исторических данных предсказать наличие дефекта на новых единицах продукции. Для этого используются как достаточно давно известные и зарекомендовавшие себя методы, так и наиболее современные, включая искусственный интеллект: градиентный бустинг, RandomForest, «простые деревья решений», «ансамбли моделей», нейронные сети.
Система слежения за металлом обеспечивает сквозную прослеживаемость и достоверность учета движения металла по технологической цепочке продукта. Она собирает информацию со всех измерителей, датчиков: скаляры, сигналы, нарушения с привязкой к единице продукта по всей длине продукта. В системе фиксируются данные о доработках, обрезках кромок, учитывается выходная длина продукта, передается информация о факте производства продукта в систему отчетности.
И, наконец, Sherlock. Система автоаттестации обеспечивает контроль всей продукции и минимизацию ошибок, связанных с человеческим фактором. Sherlock обладает инструментами для поиска первопричин отклонений по качеству, анализа трендов и построения моделей, обеспечивает доступность данных для любого пользователя, возможность быстрого подбора заказов для продуктов и продуктов для заказов. В случае неполадок система упрощает определение виновника дефекта и предоставление доступа к фотографиям дефектов поверхности. Результатами использования системы является снижение числа претензий, сокращение внутренних потерь, рост точности исполнения сроков поставок.
Если приводить конкретные примеры того, как цифровые решения могут повлиять на качество продукции, поставляемой клиенту: в рамках одного из кейсов создана модель машинного зрения, определяющая заклинивание барабана и застревание шаров. Данная мера помогла избежать претензий из-за нарушения режима закалки шаров. Это происходило из-за того, что шары заклинивали, а на конвейере есть слепые зоны, в которых человек не мог обнаружить проблему.
Другой пример: нашими специалистами было настроено автоматическое помещение оцинкованного проката в карантин с назначением испытаний на отслоение в случае отклонений в процессе оцинкования от нормативных границ и в случае аномальных значений ненормируемых параметров. Для этого была создана нейросетевая модель, которая выявляет аномалии в процессе оцинкования. После внедрения этого решения претензий от клиентов не поступало.
В результате благодаря повышению базового качества продукции при поставках точно в срок проект АСКК привел к снижению клиентских потерь от отсортировки по дефектам поставщика. Не без гордости могу сказать, что за период с 2018 по 2022 год доля поступивших претензий по четырем видам продукции, охваченных системой, снизилась на 55%.
Кстати:
«Северсталь» внедряет систему Sherlock в течение семи лет. В развитие проекта уже инвестировано 1,28 млрд рублей, а в будущем планируется вложить не менее 2 млрд. Системой в компании охвачена сквозная цепочка производства оцинкованного, горячекатаного рулонного и травленого прокатов, товарной слябы. Сейчас 4,2 млн тонн из около 10,7 млн тонн продукции проходит через систему, при этом контролируется 43% дефектов, когда-либо фигурировавших в претензиях.
Номер публикации: №38 13.10.2023