Важно на всех стадиях
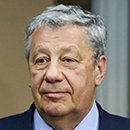
В своем обращении к участникам круглого стола вице-президент НОСТРОЙ Аркадий Чернецкий отметил сложность и многогранность обсуждавшейся проблематики. Во всем мире принципы трех «Э» реализуются в неразрывной взаимосвязи друг с другом, а тренд на сокращение расхода энергоресурсов положительно сказывается на экономике промышленных предприятий, так и существенно снижает негативное воздействие производств на окружающую среду. И хотя забота о ней — сама по себе отличная идея, важно отметить, что экологичность привлекает не только бонусами для здоровья, но и тем, что применение инновационных материалов и технологий позволяет расходовать в несколько раз раза меньше энергии, приводя к экономии средств потребителей ресурсов. Это верно для всех сфер строительства и ЖКХ, при этом все более ориентированным на энергоэффективность и экологичность становится строительство жилых домов. Для реализации всех подобных задач важно обратиться к опыту профессионалов-практиков, которые им следуют от стадии проектирования до стадии эксплуатации. «Я бы хотел, чтобы участники дискуссии акцентировали свое внимание на инновационных материалах и разработках, применяющихся на стройплощадках. Не менее важно, чтобы одновременно были рассмотрены вопросы долговечности, качества и экологичности их применения», — подчеркнул Аркадий Чернецкий.
Сухой vs мокрый
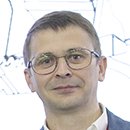
В этой связи огромное значение имеет то, что происходит в базовых отраслях промышленности строительных материалов (ПСМ) и, прежде всего, в цементной отрасли, где производство — одно из самых энергои ресурсоемких. С подробным анализом ситуации в цемпроме перед участниками круглого стола выступил технический директор инвестиционно-консалтинговой компании «СМ ПРО» Евгений Высоцкий, напомнивший, что традиционно существуют сухой, мокрый и комбинированный способы производства цемента, причем второй из них — наиболее энергозатратный и экологически вредный: при производстве клинкера по мокрому способу требуется вдвое больше ресурсов, чем по сухой технологии. До 2008 года в России не осуществлялся ввод новых цементных производств, но затем было запущено в эксплуатацию сразу несколько мощностей производительностью более 38 млн тонн продукции в год, и практически все эти технологические линии были построены по сухому способу, в результате чего его доля выросла с 20% в 2011-м до 60% в 2020-м. Однако затем были введены новые мощности на «Чеченцементе», «Якутцементе» и других предприятиях, а также восстановлено производство по мокрому способу на «Воскресенскцементе». Как следствие, доля цемента, произведенного по энергосберегающим технологиям, снизились с 60,2% в 2020 году до 58,2% в прошлом.
«Есть несколько фундаментальных причин, наличие которых не позволяет сказать, по какой технологии будет построен следующий цементный завод», — пояснил эксперт. Первая из них, по его словам, географическая. Дело в том, что уровень потребления цемента на квадратный километр территории в РФ один из самых низких: по этому показателю страна находится на 148-м месте в мире. Для примера — в 2017 году в КНДР потребление составило 574 тонны на квадратный километр, в Иране — почти 30 тонн, тогда как в России — 3,2 тонны. При этом потребление цемента в большинстве регионов не превышает 500 тыс. тонн в год. Поэтому предприятия, у которых мощность выше, вынуждены часть продукции транспортировать железнодорожным транспортом на большие, а иногда и сверхдальние расстояния, из-за чего доходность дальних продаж стремится к нулю, иногда же их рентабельность бывает и отрицательной. Для того чтобы на территории страны производство и потребление цемента было сбалансировано, нужно строить заводы небольшой мощности (в пределах 300-500 тыс. тонн цемента в год).
Вторая причина — технологическая. Отечественные производители основного цементного оборудования не способны предложить заказчикам «под ключ» технологическую линию по сухому способу, но по мокрому ее оборудовать могут. В то же время зарубежные производители не предлагают готовых комплектных решений по мокрому способу для заводов мощностью до 500 тыс. тонн цемента в год, что означает, что небольшое производство по мокрому способу будет гораздо лучше сбалансировано с рынком.
И наконец, экономическая причина кроется в том, что при нынешней стоимости топлива в стране заводы, работающие по мокрому способу, могут успешно конкурировать с энергоэффективными производствами.
Также примечательно, что наряду с ростом доли мокрого способа в России увеличивается и доля бездобавочного цемента. Так, производство портландцемента без минеральных добавок в 2022 году выросло по сравнению с 2021-м на 2,8%, производство же цемента с минеральными добавками сократилось на 4,9%. Обращает на себя внимание и значение клинкер-фактора, то есть доли клинкера в цементе: в России доля добавок сегодня составляет лишь 10%, тогда как в европейских странах и в Китае она может доходить до 30-50%.
«Сегодня доля бездобавочного цемента увеличилась до 66%, и это долгосрочный тренд, который начался с 90-х годов прошлого века. Из-за этих тенденций ни о каком серьезном вкладе цементников в снижение углеродного следа речь пока не идет», — выразил сожаление Евгений Высоцкий.
КПД на максимуме
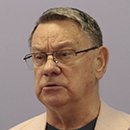
Далее с докладом по теме «Энергоэффективность производства как фактор улучшения экологии в строительстве и ЖКХ» выступил доктор технических наук Олег Богомолов — руководитель группы компаний (ГК) ИНТЕРБЛОК. В течение 25 лет инновационная продукция и решения этого предприятия успешно внедряются в России и за рубежом. ГК запатентовала несколько технологий, а ключевая ее продукция — энергоэффективные парогенераторы собственной разработки. Они являются одним из самых надежных и экономичных в своем классе оборудования по критерию «Затраты на топливо-производительность», и их эксплуатация обеспечивает кратное снижение затрат на топливно-энергетические ресурсы в себестоимости выпускаемой промышленными предприятиями продукции. Как отметил спикер, ИНТЕРБЛОК со дня своего основания руководствуется в своей деятельности принципом трех «Э», но чтобы его реализация стала действительно широкой, он должен быть воспринят всем обществом снизу до самого верха, от потребителей ресурсов ЖКХ до членов правительства. Проблема в том, что сегодня даже руководители многих предприятий плохо понимают, что такое энергоэффективность. Им сложно ее оценить, когда она рассчитывается в гигакалориях. Поэтому в ИНТЕРБЛОКЕ полагают, что в расчетах проще исходить из расхода условных кубометров газа, который, естественно, имеет свою калорийность. По оценке Олега Богомолова, в сегодняшних условиях эффективным может являться только такое производство, когда на куб железобетона используется не более 10-12 кубов природного газа. К примеру, применение парогенераторов ИНТЕРБЛОКА вместо традиционных паровых котлов при подготовке бетона дало трехкратное сокращение затрат энергии на кубометр этого материала. Такие установки сегодня успешно функционируют более чем на 60 предприятиях в России, Белоруссии, Казахстане, Киргизии и других странах.
В ЖКХ возможности для повышения энергоэффективности также огромны, ведь котельная, в работе которой используются традиционные котлы, ежегодно выбрасывает в атмосферу шесть тонн вредных веществ, а таких «кочегарок» в стране десятки тысяч. Особенность агрегатов ИНТЕРБЛОК в том, что у них нет дымовой трубы, при этом они имеют немыслимо высокий КПД в 97%. Их применение дало бы минимум двукратное снижение расхода гигакалорий при выработке тепла.
Вместе с тем эксперт признает, что подобные инновации в стране приживаются сложно: «Сегодня изобретательство и рационализаторство — не самое популярное направление. Хотя во многом благодаря ему в советский период нашей истории происходили беспрецедентные промышленные прорывы». В целом же глава ГК ИНТЕРБЛОК считает, что принципы трех «Э» являются всеобъемлющими, что это верные ориентиры для развития экономики. «Они указывают правильный путь. И когда мы ему следуем, то получается их воплотить на практике», — заключил он.
Контур без прорех
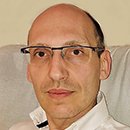
Согласился с коллегами, что тема повышения энергоэффективности сегодня как никогда актуальна, и руководитель инженерно-технического центра «Технониколь» Андрей Титов, напомнивший собравшимся в НОСТРОЙ о «свежем» постановлении правительства РФ от 9 сентября, в котором закреплены условия, при которых должна быть достигнута цель по снижению энергоемкости ВВП страны к 2035 году на 35%. «Все, что помогает приблизиться к этому показателю, должно быть востребовано, а препятствия следует убирать, — уверен специалист. — Исходя из этого, в «каскад» средств достижения целевого результата входят такие меры, как снижение себестоимости строительства и сокращение капитальных затрат на повышение теплозащиты».
По словам Андрея Титова, на законодательном уровне в этом направлении была проделана объемная работа (в числе последних по времени документов — Приказ Минстроя России №399/пр «Классы энергоэффективности жилых многоквартирных зданий» от 2016 года и Приказ Минстроя России №1550/пр «Требования энергоэффективности зданий, строений, сооружений» от 2017-го), которая заложила высокие требования к энергоэффективности сооружений. Но на деле получается, что нормативная база создана, а базовые требования определены на основании результатов расчета энергопаспорта модельного здания с уровнем теплозащиты оболочки конца прошлого века! Как следствие, из-за низкой однородности оболочки зданий и необоснованно заниженных норм теплопотерь тепловая защита сооружений, то есть размер их допустимых тепловых потерь находится на уровне 90-х годов. К тому же на практике удельная характеристика расхода тепловой энергии на отопление в расчетах подгоняется под норматив, а органы строительной экспертизы не контролируют корректность условий применения регионального коэффициента.
«Ситуация не очень хорошая, так как тарифы на тепло растут, — пояснил Андрей Титов, — и получается двойной удар по ЖКХ и затратам потребителей: с одной стороны, повышается расход энергии, а с другой — ее стоимость». Усугубляет, по его мнению, реальное положение дел и то, что, хотя практически каждое новое жилое здание при продаже квартир в нем декларируется застройщиками как дом класса А или B, в действительности в них энергии потребляется существенно больше. Это происходит вследствие того, что при отсутствии корректного учета однородности оболочки зданий неучтенные тепловые потери в них составляют до 50%. Правда, застройщики за счет применения более эффективного инженерного оборудования пытаются понизить энергопотребление в своих зданиях, но не всегда эти решения грамотные. И часто они получаются дороже, чем использование других вариантов.
Дворец из стекла
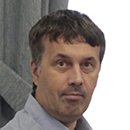
Яркий пример сочетания удачных проектировочных решений, высокой энергоэффективности и функциональности объекта, а также красивого дизайнерского проекта привел на мероприятии технический директор проектного бюро UNK project Сергей Сафронов, рассказавший о только что построенном в Москве на ВДНХ павильоне «Атом». Открытие этого «стеклянного дворца» намечено на 4 ноября. Совокупная площадь здания составляет 25 тыс. квадратных метров, и оно рассчитано на одновременное комфортное пребывание в нем 4,5 тыс. человек. Поэтому естественно, что высокие энергоэффективные характеристики павильона закладывались еще на уровне проработки архитектурной концепции. Учитывая, что два стеклянных фасада «Атома» имеют протяженность в 150 метров, с точки зрения энергоэффективности важна даже ориентация павильона в пространстве. Он повернут на север, и сама его «посадка» помогает экономить ресурсы. Естественно, павильон насыщен энергоэффективным оборудованием. Так, в его нижней части установлены тепловые конвекторы, а наверху — вентиляционное оборудование. Такая схема размещения климатической техники позволяет избежать запотевания стекла и обеспечивает работу верхнего подвижного узла, а также помогает надежному сочленению стеклянного фасада и консольной «зеленой» кровли.
В целом же, по мнению Сергея Сафронова, энергоэффективность заключается не только в применении инновационных технологий — для ее достижения необходимо реализовать комплекс мер, направленных на снижение энергопотребления здания. В павильоне «Атом» на повышение энергоэффективности будут «работать» правильная эксплуатация систем отопления, вентиляции и кондиционирования воздуха, оптимизация систем освещения. В решении этих вопросов также будет помогать система автоматизации и диспетчеризации здания. Эти же решения должны применяться и в других проектах.
Роботизация по максимуму
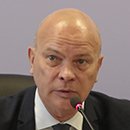
Не менее важным является использование в зданиях современного энергоэффективного подъемного оборудования. На этих аспектах остановился представитель Серпуховского лифтостроительного завода (СЛЗ) Владимир Самойлов. СЛЗ начал работу в декабре 2022-го, и, как сообщил спикер, к концу текущего года предприятие должно выпустить первую тысячу лифтов. Потенциально завод способен производить 13 тыс. лифтов в год.
СЛЗ оснащен наиболее передовым станочным парком в стране, а на его территории имеется самая высокая в России испытательная башня, в которой можно одновременно проводить испытания до девяти лифтов, движущихся со скоростью до восьми метров в секунду. Оборудование завода максимально экологично, например, специальная покрасочная камера работает так, что нет выбросов в атмосферу. СЛЗ делает акцент на роботизации производства лифтов, сварочное оборудование полностью автоматизировано, а применение в изделиях энергоэффективных узлов, например, безредукторных лебедок, обеспечивает снижение расхода электроэнергии при их эксплуатации до 50%.
«В лифтостроении важна надежность, гарантирующая полное отсутствие рисков для будущих пользователей, — подчеркнул Владимир Самойлов. — Поэтому процессы производства на заводе роботизированы по максимуму, автоматизация позволяет устранять риски, связанные с человеческим фактором. Например, там, где стандарты допускают варить вручную, мы подключаем роботизированный сварочный станок».
Преобразователи чугуна
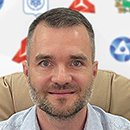
Интересные энергоэффективные решения представил на встрече генеральный директор производственно-строительной компании (ПСК) «ТомБат» Иван Шишков. Его предприятие накопило большой производственный «3Э-опыт» по восстановлению радиаторов отопления. Разработанная и проверенная на практике инновационная технология ПСК по отбраковке вторичного сырья помогает вернуть на рынок стройматериалов 71% чугунных батарей.
Основной принцип, которым руководствуются в «ТомБате», — Win-Win. Он применяется во всех сферах взаимодействия компании, включая работы с клиентами и поставщиками, а также внутри коллектива. Уже сегодня ПСК не допускает отправки более тысячи тонн в год старых батарей на металлургические заводы для последующей переплавки, тем самым уменьшая выбросы вредных веществ в атмосферу. Таким образом, используемая технология отбраковки чугунных радиаторов вносит значимый вклад в защиту окружающей среды. Ее применение очень перспективно, так как она способна понизить затраты бюджета на реализацию таких национальных проектов, как «Экология» и «Чистый воздух». Несомненно, полезно ее использовать в программе реновации Москвы и в региональных программах по капремонту систем отопления в социальных учреждениях и жилом фонде страны.
Как отметил Иван Шишков, в столице, к примеру, предстоит снести более 5 тыс. «хрущевок», демонтировав в них примерно 60 тыс. тонн чугунных радиаторов. Сейчас эти радиаторы продаются на пункты приема черных металлов, далее направляются в переплавку на металлургические комбинаты, итог — загрязнение окружающей среды. «На данном уровне модернизации и развития нашего производства мы способны переработать этот объем за 10 лет (как раз до конца утвержденной программы реновации Москвы в 2032 году) и гарантированно не допустить в переплавку 71% от него, — заявил глава «ТомБат», — а это 42,6 тыс. тонн восстановленных радиаторов отопления, которые прослужат еще более 30 лет. При реализации такого подхода столичный бюджет получит экономию средств в размере более миллиарда рублей».
Номер публикации: №37 06.10.2023